Sponsored article
How do I prepare plastic for sealing?
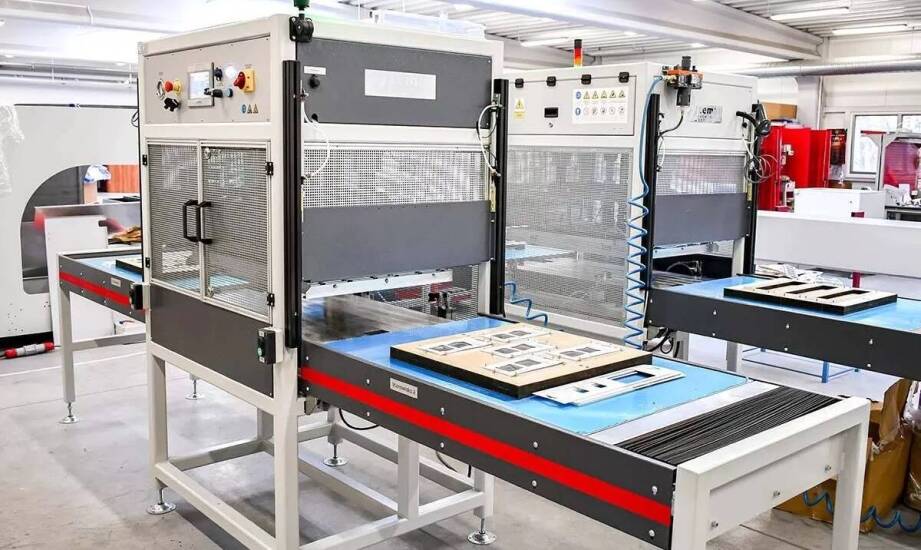
Plastic sealing is a method of permanently joining materials through the use of heat, pressure and sometimes additional factors. In order to achieve a high-quality joint, it is essential that the material surface is properly prepared. This process requires accuracy and knowledge of the properties of the material to be sealed.
Cleaning the material surface
The first step in preparing the plastic for sealing is to remove any contamination from its surface. Dust, oil, grease or production residues can significantly reduce the quality of the joint. Cleaning is carried out with specialised chemicals, such as isopropyl alcohols, which evaporate without leaving a residue. In some cases, mechanical cleaning methods such as gentle sanding of the surface can be used to remove more stubborn dirt. Plastic sealing equipment is available from Zemat Technology Group.
Checking and aligning edges
The edges of the parts to be sealed must be perfectly aligned and even to ensure an even joint along the entire length. Smooth and even edges minimise the risk of gaps, which is crucial for the durability and strength of the joint.
Verification of material properties
Each type of plastic has different properties, such as melting point, reaction to heat or elasticity. Before sealing, ensure that the material is suitable for the chosen method. It is worth checking the markings and technical specifications of the material to adjust process parameters such as temperature, time, and pressure. An inappropriate choice of parameters can lead to material damage or inadequate joining.
Importance of technical parameters and process automation
Modern industrial sealer machines, such as the Terma series models, allow precise control of the sealing process, which translates into repeatability and quality of the seal. Models such as the Terma R, used for the production of blister packs, for example, use a pneumatic drive and digital control to streamline preparation for sealing and allow for quick changeovers. With these solutions, the plastic preparation process can be better integrated into production, increasing efficiency and reducing the risk of errors.
In addition, Zemat’s sealer machines meet all safety and quality standards, ensuring process stability and a long service life for the equipment.